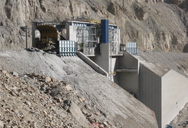
Ball mill upgrade cuts energy consumption by 25% - FLSmidth
Upgrading an existing ball mill circuit with hydraulic roller presses and TRIBOMAX® wear surfaces achieved a 127% increase in production, at the same time as lowering power consumption by 25%, at JK Cement’s Mangrol cement plant.
More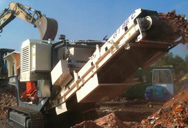
Modelling SAG milling power and specific energy consumption
For example, for an 36′ × 17′ SAG Mill, with a power consumption of
More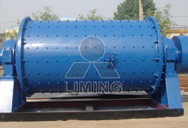
Performance optimization of an industrial ball mill for ... - SciELO
The ball mill consumes about 25-30% of the total energy in the beneficiation plant, and
More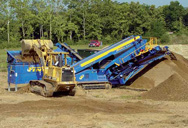
Ball Mill Design/Power Calculation - 911 Metallurgist
The power consumption per short ton will only be correct for the specified size reduction when grinding wet in closed circuit. If the
More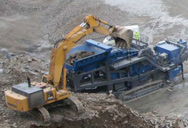
Design of horizontal ball mills for improving the rate of ...
The power consumption of a ball mill is one of the most important parameters to consider in the design of a ball mill because it determines its economic efficiency. The power consumption is usually determined by charge fill level, lifter height, lifter number, and mill speed.
More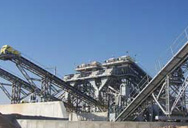
Charge behaviour and power consumption in ball mills:
Discrete element method (DEM) modelling has been used to systematically study the effects of changes in mill operating parameters and particle properties on the charge shape and power draw of a 5-m ball mill. Specifically, changes in charge fill level, lifter shape (either by design or wear) and lifter pattern are analysed. The effects of
More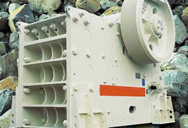
Performance optimization of an industrial ball mill for ... - SciELO
The ball mill consumes about 25-30% of the total energy in the beneficiation plant, and hence any improvement will improve the overall economics of the plant. The power consumption of the ball mill was monitored for two months, and the data is shown in the histogram in Figure 2c.
More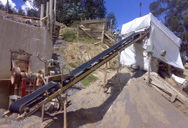
Improving the Efficiency of the Coal Grinding Process in Ball
The power consumption for the preparation can be reduced up to 5 % for the selected operation mode of the grinding facility. ... Angel and Baydusenov, Galym, Improving the Efficiency of the Coal Grinding Process in Ball Drum Mills at Thermal Power Plants (February 24, 2022).
More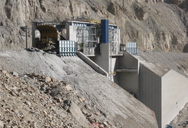
Ball mill upgrade cuts energy consumption by 25% - FLSmidth
Upgrading an existing ball mill circuit with hydraulic roller presses and TRIBOMAX® wear surfaces achieved a 127% increase in production, at the same time as lowering power consumption by 25%, at JK Cement’s Mangrol cement plant.
More
Calculation method and its application for energy consumption of ball
Calculation method and its application for energy consumption of ball mills in ceramic industry based on power feature deployment February 2020 Advances in Applied Ceramics 119(4):1-12
More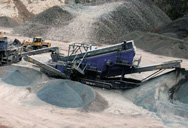
Ball Mills - 911 Metallurgist
A ball mill efficiently operated performs a wide variety of services. In small milling plants, where simplicity is most essential, it is not economical to use more than single stage crushing, because the Steel
More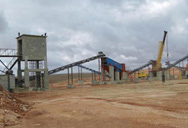
Energy Use of Fine Grinding in Mineral Processing SpringerLink
This quantity is small compared to the power used by a semi-autogenous mill and a ball mill in a primary grinding circuit; a ball mill can have an installed power of up to 15 MW, while installed power for a SAG mill can go up to 25 MW. However, the energy used for fine grinding is still significant.
More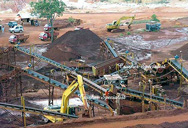
Estimating Ball Consumption - Molycop
For an improved understanding, the wear rate constant is directly related to the grinding media consumption rate expressed in grams of steel per kWh drawn by the mill, using the simple expression: where
More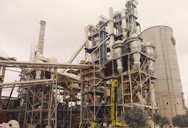
Ten Ways to Improve the Grinding Efficiency of Your Ball Mill
Here are ten ways to improve the grinding efficiency of ball mill. 1. Change the original grindability The complexity of grindability is determined by ore hardness, toughness, dissociation...
More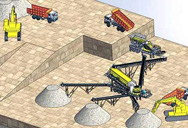
Steel Balls Consumption Ball Mill Effect - JXSC Machine
Tips for Reducing Energy Consumption of Steel Balls in Ball Mills 1. Change the grindability of iron ore The particle size distribution of the raw materials fed into the ball mill is the first reason that affects the energy
More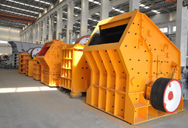
Power Calculation of Ball-Tube Mill Drives in the Construction ...
The most energy-intensive process is grinding. The main equipment for grinding construction materials are ball-tube mills, which are actively used in industry and are constantly being improved. The main issue of improvement is to reduce the power consumption of a ball-tube mill with cross-longitudinal movement of the load.
More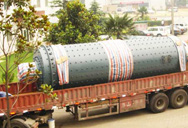
Improving energy efficiency in comminution - MINING.COM
Comminution uses at least three percent of total global electricity production and according to the Coalition for Energy Efficient Comminution, it accounts, on average, for more than 50 percent of...
More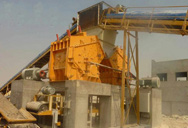
Ten Ways to Improve the Grinding Efficiency of Your Ball Mill
Here are ten ways to improve the grinding efficiency of ball mill. 1. Change the original grindability. The complexity of grindability is determined by ore hardness, toughness, dissociation and structural defects. Small grindability, the ore is easier to grind, the wear of lining plate and steel ball is lower, and the energy consumption is also ...
More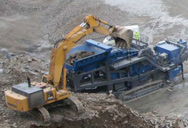
Design of horizontal ball mills for improving the rate of ...
The power consumption of a ball mill is one of the most important parameters to consider in the design of a ball mill because it determines its economic efficiency. The power consumption is usually determined by charge fill level, lifter height, lifter number, and mill speed.
More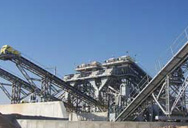
Charge behaviour and power consumption in ball mills:
Discrete element method (DEM) modelling has been used to systematically study the effects of changes in mill operating parameters and particle properties on the charge shape and power draw of a 5-m ball mill. Specifically, changes in charge fill level, lifter shape (either by design or wear) and lifter pattern are analysed. The effects of
More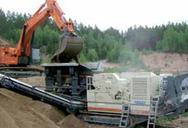
Addition of pebbles to a ball-mill to improve grinding efficiency ...
The average saving in energy consumption was about 13% and a saving in ball consumption of 25% applies. ... and to maximize power draw. Overflow ball-mills are often used and a mixture of ball sizes is used to top up the ball charge at regular intervals, e.g. the KCGM Mt Charlotte circuit in Australia used a mixture of 70 mm and 60
More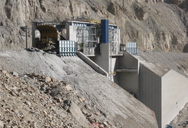
Ball mill upgrade cuts energy consumption by 25% - FLSmidth
Upgrading an existing ball mill circuit with hydraulic roller presses and TRIBOMAX® wear surfaces achieved a 127% increase in production, at the same time as lowering power consumption by 25%, at JK Cement’s Mangrol cement plant.
More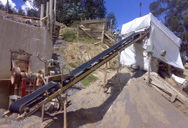
Improving the Efficiency of the Coal Grinding Process in Ball
The power consumption for the preparation can be reduced up to 5 % for the selected operation mode of the grinding facility. ... Angel and Baydusenov, Galym, Improving the Efficiency of the Coal Grinding Process in Ball Drum Mills at Thermal Power Plants (February 24, 2022).
More
Calculation method and its application for energy consumption of ball
Calculation method and its application for energy consumption of ball mills in ceramic industry based on power feature deployment February 2020 Advances in Applied Ceramics 119(4):1-12
More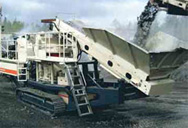
Power Calculation of Ball-Tube Mill Drives in the Construction ...
The main issue of improvement is to reduce the power consumption of a ball-tube mill with cross-longitudinal movement of the load. A comparative analysis and the possibility of using the known methods for calculating the power consumption of the drive of a ball-tube mill with cross-longitudinal movement of grinding bodies is given.
More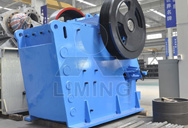
Calculation method and its application for energy
The energy consumption of the ball mills can bedetermined by the power consumption and operatingtime of the mill. Here, the power is calculated bymultiplying the electric current and...
More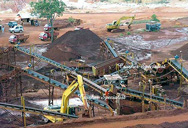
Estimating Ball Consumption - Molycop
For an improved understanding, the wear rate constant is directly related to the grinding media consumption rate expressed in grams of steel per kWh drawn by the mill, using the simple expression: where
More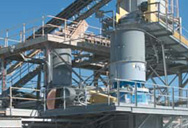
10 Ways to Improve the Grinding Efficiency of Your Ball Mill
Here are the 10 ways for your to improve the ball mill performance: Step#1. Change the original grindability. Step#2. More crushing and less grinding to reduce the feed size into mill. Step#3. Reasonable filling rate of steel ball. Step#4. Reasonable size and proportion of steel ball.
More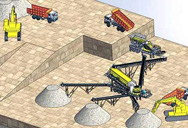
Steel Balls Consumption Ball Mill Effect - JXSC Machine
Tips for Reducing Energy Consumption of Steel Balls in Ball Mills 1. Change the grindability of iron ore The particle size distribution of the raw materials fed into the ball mill is the first reason that affects the energy
More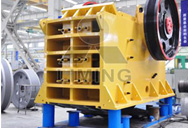
Addition of pebbles to a ball-mill to improve grinding efficiency
This scenario assumes that the mills adoption rate of this technology starts to linearly increase from 0% in 2020 and reach 100% by 2030. The scenarios IR-PAG and GO-PAG assume 13% energy savings and 25% reduction in ball consumption (Nkwanyana and Loveday, 2017), achieved by the addition of pebbles to ball mills in
More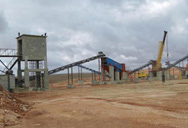
Energy Use of Fine Grinding in Mineral Processing SpringerLink
This quantity is small compared to the power used by a semi-autogenous mill and a ball mill in a primary grinding circuit; a ball mill can have an installed power of up to 15 MW, while installed power for a SAG mill can go up to 25 MW. However, the energy used for fine grinding is still significant.
More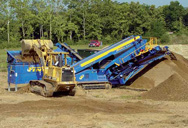
Effect of lifters and mill speed on particle behaviour, torque, and ...
The power consumption of a ball mill is one of the most important parameters to consider in the design of a ball mill because it determines its economic efficiency. The power consumption is usually determined by charge fill level, lifter height, lifter number, and mill speed.
More