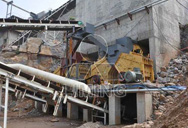
Iron Ore Sintering Part 2. Quality Indices And Productivity
Iron Ore Sintering Part 2. Quality Indices And Productivity Authors: Javier Mochón ALEJANDRO CORES I. Ruiz-Bustinza E.T.S. of Mining and Energy
More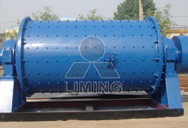
IRON ORE SINTERING PART 2. QUALITY INDICES AND
The iron ore used presents a low MgO content (0.01%) and a high Al2O3 content (2.99%). It was seen that raising the MgO content in the sinter, from 1.4 to 2.6%, increased the
More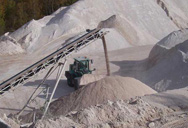
IRON ORE SINTERING PART 2. QUALITY INDICES AND
doi: 10.15446/dyna.v81n183.41568 corpus id: 53474991; iron ore sintering part 2. quality indices and productivity @article{mochn2014ironos, title={iron ore sintering part 2.
More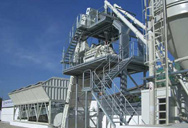
IRON ORE SINTERING PART 2. QUALITY INDICES AND
Sinter plants have to process mineral mixes in order to obtain sinter of a suitable composition and quality to be loaded into the blast furnace. For this purpose a series of
More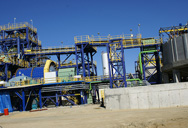
IRON ORE SINTERING PART 2. QUALITY INDICES AND
The iron ore used presents a low MgO content (0.01%) and a high Al2O content (2.99%). It was seen that raising 3 the MgO content in the sinter, from 1.4 to 2.6%, increased the
More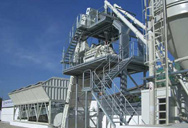
(PDF) Iron Ore Sintering: Quality Indices - ResearchGate
Sinter plants process a mixture of iron ore fines, recycled ironmaking products, slag-forming agents and solid fuel (coke) with the finality of obtaining a product
More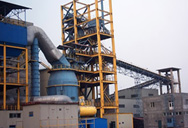
Iron ore sintering part 2. quality indices and productivity
Sinter is subjected to in-depth characterisation in terms of chemical and granulometric analysis, determination of the mineral phases in its structure and of quality
More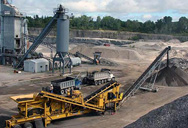
Iron Ore Sintering: Quality Indices - Taylor Francis Online
Sinter characterization includes chemical and granulometric analysis, determination of the mineral phases in its structure, apart from a series of quality
More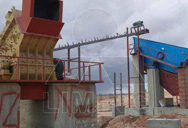
(PDF) Iron ore sintering. Part 1. Theory and practice of the
Sintering is a process where a mixture of ore, flux and coke is agglomerated (agglomerated) in the sinter plant to produce suitable sintered products in
More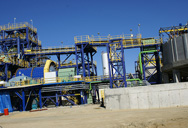
SINTERIZACIÓN DE MINERALES DE HIERRO PARTE 2. ÍNDICES DE
IRON ORE SINTERING PART 2. QUALITY INDICES AND PRODUCTIVITY SINTERIZACIÓN DE MINERALES DE HIERRO PARTE 2. ÍNDICES
More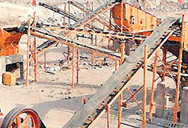
Iron Ore Sintering: Quality Indices - Taylor Francis Online
ABSTRACT. Sinter plants process a mixture of iron ore fines, recycled ironmaking products, slag-forming agents and solid fuel (coke) with the finality of obtaining a product with the suitable characteristics (thermal, mechanical, physical, and chemical) for being fed to the blast furnace.
More
IRON ORE SINTERING PART 2. QUALITY INDICES AND
The iron ore used presents a low MgO content (0.01%) and a high Al2O3 content (2.99%). It was seen that raising the MgO content in the sinter, from 1.4 to 2.6%, increased the FeO content and decreased productivity and the RI, RDI and TI indices [13]. 2.1.4. CaO sinter
More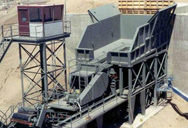
Iron ore sintering part 2. quality indices and productivity
Iron ore sintering part 2. quality indices and productivity. 41568-194762-1-PB.pdf (997.2Kb) Autor. Mochón, Javier. Cores, Alejandro. Ruiz Bustinza, Íñigo ... It is also important to operate sinter plants with high productivity and to ensure a uniform sinter composition and quality so as to facilitate the steady state operation of the blast ...
More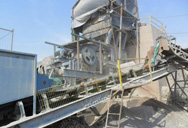
Sintering SpringerLink
Fernández-González et al. : Iron ore sintering: Quality indices, where the indices used to define the quality of the sintered product to ensure blast furnace stable, homogeneous, and ... Ferreira S, Ruiz-Bustinza I, Mochón J (2013): Iron ore sintering. Part 1. Theory and practice of the sintering process. DYNA 80(180):152–171. Google Scholar
More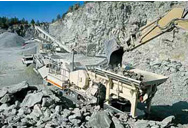
Iron Ore Sintering: Quality Indices Semantic Scholar
Iron Ore Sintering: Quality Indices Semantic Scholar ABSTRACT Sinter plants process a mixture of iron ore fines, recycled ironmaking products, slag-forming agents and solid fuel (coke) with the finality of obtaining a product with the suitable characteristics (thermal, mechanical, physical, and chemical) for being fed to the blast
More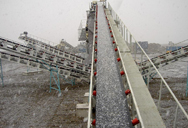
Sintering Properties and Optimal Blending Schemes of Iron Ores
In order to obtain good sintering performance, it is important to understand sintering properties of iron ores. Sintering properties including chemical composition, granulation and high-temperature behaviors of ores from China, Brazil and Australia. Furthermore, several indices were defined to evaluate sintering properties of iron ores.
More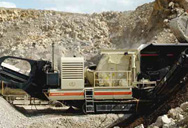
Figure. 1. Optimised sinter structure (x1100). H
Iron Ore Sintering Part 2. Quality Indices And Productivity Article Full-text available Jan 2014 Javier Mochón ALEJANDRO CORES I. Ruiz-Bustinza JOSÉ IGNACIO ROBLA Sinter plants have to process...
More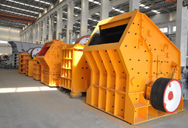
Iron Ore Sintering Part 2. Quality Indices and Productivity
Iron Ore Sintering Part 2. Quality Indices and Productivity. Luis Verdeja ...
More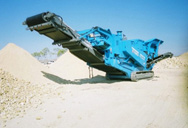
IRON ORE SINTERING PART 2. QUALITY INDICES... - Course Hero
The iron ore used presents a low MgO content (0.01%) and a high Al2O3content (2.99%). It was seen that raising the MgO content in the sinter, from 1.4 to 2.6%, increased the FeO content and decreased productivity and the RI, RDI and TI indices [13]. 2.1.4.
More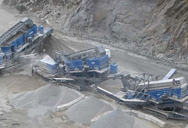
Iron ore sintering. Part 3: Automatic and control systems - SciELO
The importance of sintering plants lies not only in their ability to take advantage of the finest iron ore granulometries, but also their capacity to recycle waste products generated throughout the ironmaking industry without altering the required physical, chemical and mechanical properties of the sinter loaded into blast furnaces [17,18].
More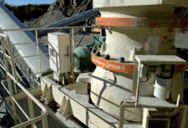
Intensified sifting feeder (ISF) Download Scientific
Iron Ore Sintering Part 2. Quality Indices And Productivity Article Full-text available Jan 2014 Javier Mochón ALEJANDRO CORES I. Ruiz-Bustinza JOSÉ IGNACIO ROBLA Sinter plants have to process...
More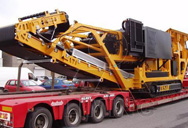
Processes Free Full-Text Experimental Production of Iron
The iron ore sintering tests described in this article enable assessment of the impact of char from waste car tires on the resulting sinter quality while maintaining the appropriate process effectivity. Waste car tires are thermally converted in the pyrolysis process that produces the char.
More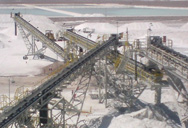
Iron ore sintering. Part 3: Automatic and control systems
charge density control to achieve uniform sintering across the width of the strand and pallet speed control to maintain optimum productivity and sinter quality [2]. It is also very important to control sinter plant gas emissions, which are produced in large volumes and contain a high number of pollutant substances with different degrees of ...
More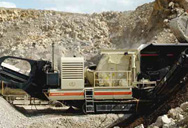
Determining the Interactions Between Raw Sinter Blend and Sinter
IRON ORE SINTERING PART 2. QUALITY INDICES AND PRODUCTIVITY J. Mochón, A. Cores, Í. Ruiz-Bustinza, L. Verdeja, J. Robla, F. García‐Carcedo Materials Science 2014 Sinter plants have to process mineral mixes in order to obtain sinter of a suitable composition and quality to be loaded into the blast furnace.
More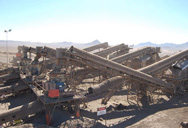
Iron Ore Sintering: Quality Indices - Taylor Francis Online
Sinter characterization includes chemical and granulometric analysis, determination of the mineral phases in its structure, apart from a series of quality indices that includes reducibility, low temperature degradation, reduction degradation and Tumbler.
More
IRON ORE SINTERING PART 2. QUALITY INDICES AND
The iron ore used presents a low MgO content (0.01%) and a high Al2O3 content (2.99%). It was seen that raising the MgO content in the sinter, from 1.4 to 2.6%, increased the FeO content and decreased productivity and the RI, RDI and TI indices [13]. 2.1.4. CaO sinter
More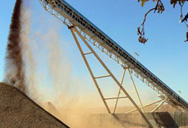
Iron ore sintering part 2. quality indices and productivity
Sinter is subjected to in-depth characterisation in terms of chemical and granulometric analysis, determination of the mineral phases in its structure and of quality indices such as reducibility, low temperature degradation, reduction degradation, and tumbler strength.
More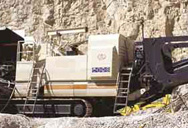
Integral Quality Index for Iron Ore Raw Materials and Cast Iron ...
IOR Criteria and Quality Indices A criterion “metallurgical value (iron ore raw material)” is used in the domestic economy since the 1960s. In economic calculations this criterion is used as a rule in the form of a coefficient with dimensionality “fractions of one,” “%,” and “points.”
More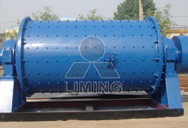
Sintering SpringerLink
The different quality indices are described and analyzed considering the influence of Fe 2 O 3, Fe 3 O 4, FeO, CaO, Al 2 O 3, SiO 2, and MgO (as well as the alkalis): softening-melting test, as it is used to simulate the behavior of iron oxides in the cohesive zone of the blast furnace; Tumbler index, as it is used to describe the cold
More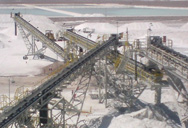
Iron ore sintering. Part 3: Automatic and control systems
charge density control to achieve uniform sintering across the width of the strand and pallet speed control to maintain optimum productivity and sinter quality [2]. It is also very important to control sinter plant gas emissions, which are produced in large volumes and contain a high number of pollutant substances with different degrees of ...
More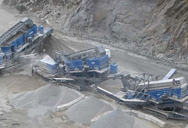
Iron ore sintering. Part 3: Automatic and control systems - SciELO
The importance of sintering plants lies not only in their ability to take advantage of the finest iron ore granulometries, but also their capacity to recycle waste products generated throughout the ironmaking industry without altering the required physical, chemical and mechanical properties of the sinter loaded into blast furnaces [17,18].
More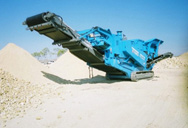
IRON ORE SINTERING PART 2. QUALITY INDICES... - Course Hero
The iron ore used presents a low MgO content (0.01%) and a high Al2O3content (2.99%). It was seen that raising the MgO content in the sinter, from 1.4 to 2.6%, increased the FeO content and decreased productivity and the RI, RDI and TI indices [13]. 2.1.4.
More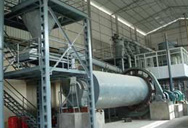
Portal de Revistas UN. DOI: 10.15446/dyna.v81n183.41568 - Crossref
IRON ORE SINTERING PART 2. QUALITY INDICES AND PRODUCTIVITY MOCHÓN, JAVIER et al. DYNA(2014),81(183): 168 https://doi/10.15446/dyna.v81n183.41568 Este artículo o revista está disponible en múltiples sitios. Por favor, seleccione un sitio para acceder a texto completo o ver otras opciones. Leer en Portal de Revistas UN Leer en
More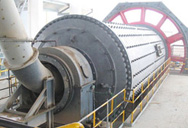
Iron Ore Sintering: Process - Taylor Francis Online
The purpose of the sintering process is manufacturing a product with the suitable characteristics (thermal, mechanical, physical and chemical) to be fed to the blast furnace. The process has been widely studied and researched in the iron and steelmaking industry to know the best parameters that allow one to obtain the best sinter quality.
More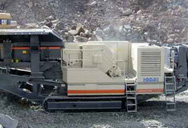
ISO 3082:2017 (en), Iron ores — Sampling and sample preparation
ISO 4696-2, Iron ores for blast furnace feedstocks — Determination of low-temperature reduction-disintegration indices by static method — Part 2: Reduction with CO and N2 ISO 4698, Iron ore pellets for blast furnace feedstocks — Determination of
More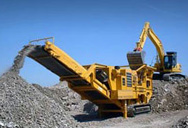
Iron ore pricing explained - Fastmarkets
Iron ore is a non-fungible commodity, and its quality varies. To help facilitate price adjustment for differences between expected and delivered product specifications, PRAs have developed value-in-use (VIU) indices for the key price-affecting chemical components of iron ore - iron, silica, alumina and phosphorus.
More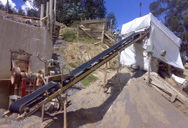
Iron Ore Agglomeration Technologies IntechOpen
Sintering is a thermal process (1300–1400°C) by which a mixture of iron ore, return fines, recycled products of the iron and steel industry (mill scale, blast furnace dusts, etc.), slag-forming elements, fluxes and coke are agglomerated in a sinter plant with the purpose of manufacturing a sintered product of a suitable chemical composition,
More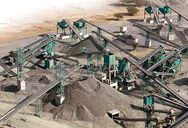
Sinter plant - Wikipedia
Sintering the material Circle cooler for cooling hot sinter Material is put on a sinter machine in two layers. The bottom layer may vary in thickness from 30 to 75 millimetres (1.2 to 3.0 in). A 12 to 20 mm sinter fraction is used,
More