
Manufacturing of aluminum flake powder from foil scrap by dry
Aluminum flake powder can be produced using aluminum foil scrap in the dry ball milling process. During the ball milling the foil is laminated, micro-forged, cracked continuously, and then finally formed into a flake shape powder.
More
Manufacturing of aluminum flake powder from foil scrap by dry
Aluminum flake powder can be produced using aluminum foil scrap in
More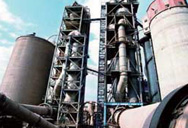
Production of Aluminum Flake Pigments by Ball Mill - ResearchGate
The work described in this paper deals with the production of aluminum
More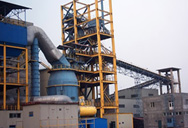
Manufacturing of Aluminum Flake Powder From Foil Scrap by Dry
In the study of Hong et al. (2000), they produced flake powder from
More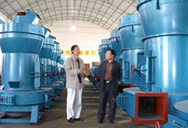
Superior Mechanical Performance of Inductively Sintered Al/SiC
In 2011, for the first time, Jiang et al. 38 reported a new approach they called it flake powder metallurgy, in which aluminum flakes with formed Al 2 O 3 skins on top can be used as bases to ...
More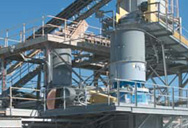
Study on Preparation, Application and Modification of Flake Aluminium ...
25.2.1 The Preparation of Flake Al Flake Al were prepared by bidirectional rotation mill. The grinding time of Al powder was 2.5 h (flake Al-1) and 7 h (flake Al-2), respectively. 25.2.2 The Preparation of Solid Propellants Solid propellants were prepared by screw extrusion technology.
More
Manufacturing of aluminum flake powder from foil scrap by dry ball ...
Aluminum flake powder can be produced using aluminum foil scrap in the dry ball milling process. During the ball milling the foil is laminated, micro-forged, cracked continuously, and then finally formed into a flake shape powder.
More
Effects of disc milling parameters on the physical properties and ...
Manufacturing of aluminum flake powder from foil scrap by dry ball milling process J. Mater. Process. Technol. (2000) A. Mahboubi Soufiani et al. Fabrication and characterization of nanostructured Ti6Al4V powder from machining scraps Adv. Powder Technol. (2010) W. Zhang et al. A literature review of titanium metallurgical
More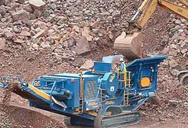
Manufacturing of Aluminum Flake Powder From Foil Scrap by Dry Ball
In the study of Hong et al. (2000), they produced flake powder from aluminum foil scrap by dry ball milling process using an inert argon and oxygen, and found that the size and shape...
More
Production of Aluminum Flake Pigments by Ball Mill
The work described in this paper deals with the production of aluminum flake powder utilities the gas atomized aluminum powder of highly an pure source. Flake pigments are produced...
More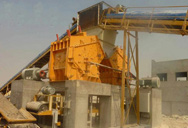
Aluminum Pigments for Powder Coatings - Silberline
The manufacture of aluminum pigments involves a specialized ball-milling process as the first stage. Here the atomized aluminum is ball-milled in the presence of solvent and a lubricant for a period of five to 40 hours. The lubricant is employed to prevent “cold welding” of the aluminum particles and thus avoid agglomerates.
More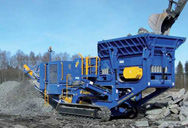
HIGHLY VERSATILE ALUMINUM FLAKE - American Coatings
the aluminum powder (grit) and hammers it into a lake shape. Typical ball milling processes will have three main ingredients: aluminum grit, a hydrocarbon solvent, and a lubricant. The pur-pose of the hydrocarbon solvent and the lubri-cant is to minimize the amount of water in the mill, thereby reducing oxidation and decreasing the probability ...
More
Ball milling: a green technology for the preparation and ...
The ball mill Ball milling is a mechanical technique widely used to grind powders into ne particles and blend materials.18 Being an environmentally-friendly, cost-effective technique, it has found wide application in industry all over the world. Since this mini-review mainly focuses on the conditions applied for the prep-
More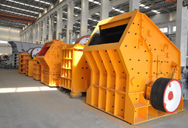
Manufacturing of aluminum flake powder from foil scrap by dry ball ...
A larger ball is more beneficial to the milling of aluminum foil into the flake powder due to the large impact energy during the falling of the ball. Intermediate stops during the ball milling produced a finer aluminum flake powder than non-stop milling for up to 25 h due to cooling of the vial.
More
Aluminum Paste Eckart NAFTA
Within the ball mill, aluminum is shaped in to flake-like particles. The process is referred to ass wet-milling, as lubricants are added to perform as a grinding aid. The milling parameters and the lubricant are determined by the application for which the pigment is
More
Free Full-Text Progress of Flake Powder Metallurgy Research
Conventional Flake Powder Metallurgy (C-FPM) The FPM via typical dry milling is introduced as powder BM in a dry jar. Specifically, the ingredients blended in the jar are reinforcement, matrix powder, steel balls, and usually a processing agent such as stearic acid, ethanol or similar.
More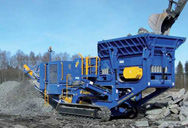
Aluminum Pigments for Plastics - Silberline
Columbia University developed the wet ball milling method. This process carries out the ... Dry aluminum flake, when suspended in air as a fine dust, has the potential for causing an ... prevent an explosion is to make certain that the aluminum does not turn into a dry powder that becomes airborne at any point during the process. Once the ...
More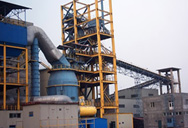
Highly Versatile Aluminum Flake for Water, Solvent and Ultra
To achieve the desirable platelet shape, aluminum pigments are traditionally produced via ball milling. Ball milling is a process whereby a horizontal mill is loaded with media and aluminum powder. As the mill rotates, the media impacts the aluminum powder (grit) and hammers it into a flake shape. Typical ball milling processes will have three ...
More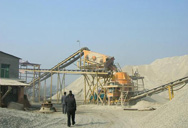
Viscous Solvent-Assisted Planetary Ball Milling for the
TEM image of BNNS-100 subjected to traditional dry ball milling shows small thick flakes. 0.23 PaS 0.64 PaS 1.43 PaS ... After 24 h of planetary ball milling, no obvious powder residue was found at the condition of 20% and 30% solid contents (Figure S6) ... and the process is similar to that of dry ball milling and results in small size ...
More
Production of Aluminum Flake Pigments by Ball Mill
The work described in this paper deals with the production of aluminum flake powder utilities the gas atomized aluminum powder of highly an pure source. Flake pigments are produced...
More
Seong-Hyeon Hong - ResearchGate
After ball milling the mixture into a fine powder, the mixture was heated up to 1373–1573 K in a carbon mold by applying a pulsed electric current, and the temperature... View +3 Study on the...
More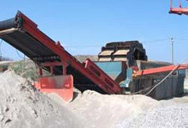
Aluminum Pigments for Plastics - Silberline
It is this process, along with the length of milling, that differentiates one grade from another. The oversized flakes are returned to the ball mill for further processing, while remaining aluminum flakes pass into a filter press. Excess solvent is removed in the process, resulting in a filter cake having a volatile content of approximately 20%.
More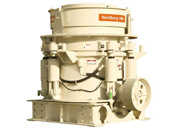
Highly Versatile Aluminum Flake for Water, Solvent and Ultra
Ball milling is a process whereby a horizontal mill is loaded with media and aluminum powder. As the mill rotates, the media impacts the aluminum powder (grit) and hammers it into a flake shape. Typical ball milling processes will have three main ingredients: aluminum grit, a hydrocarbon solvent, and a lubricant.
More
Ball milling: a green technology for the preparation and ...
Ball milling is a mechanical technique widely used to grindpowders into ne particles and blend materials.18Being anenvironmentally-friendly, cost-effective technique, it has foundwide application in industry all over the world.
More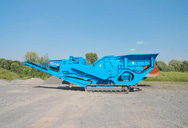
(PDF) The homogenizing of carbon nanotube dispersion in aluminium
The initial mix of powders comprising the AA2024 alloy applied in this study are shown in Figure 1a. The obtained AA2024 powder after the ball-milling process presented a flake-shaped...
More
Wet Milling vs Dry Milling: The Differences, Advantages
The industrial milling process helps to maximize the yield of the mix’s ingredients and can improve the resulting product’s functionality as well. For example, milling can help improve color development, film properties, and product flow in inks and paints. Understanding the difference between wet milling and dry milling
More
High Energy Ball Milling - Stirred Ball Mill - Union Process
The savings in energy and the increase in grinding efficiency provided by Attritors are substantial. The graph below compares various mills during the high energy ball milling process. Select a link to learn more about these Attritor-style stirred ball mills: Dry Grinding – Continuous or Batch Mode. Dry Grinding – Continuous Mode.
More
Journal of advanced materials and processing - Magiran
Processing of aluminum flake powder via high energy ball milling under different conditions reaching to aluminum nanoparticles Mohamed Saad *, Iman Ghoneim, Al Sayed Al Sherbini Pages 31-42 Abstract Research/Original Article Original: English
More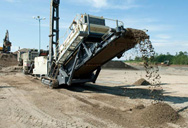
Superior Mechanical Performance of Inductively Sintered Al/SiC
The ball milling intensity increases, inducing a higher compressive force and resulting in more accelerated fracturing and welding. Consequently, the morphology of this powder is converted...
More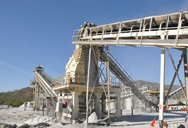
dry ball milling process Mining Quarry Plant
Dry grind processing, ball mill for manufacturing aluminum Aluminum flake powder is widely used in ngerprint detection, aerated lightweight concrete, paint component for automobile and industrial applications, additive for Horizontal Ball Mill-Horizontal Ball Milling For Dry Mill Process
More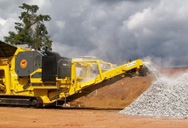
Methods to Re-Use and Recycle Aluminium Machining Swarf
During this treatment, the aluminium oxide layer reacts with the acid/hydroxide and thus exposes the pure aluminium. which then oxidises, however this fresh oxide layer is uniform making swarf suitable for powder production.
More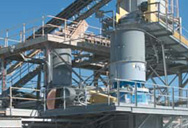
Effect of Ball Milling Mechanism on the Density and Hardness
Two mechanisms, low-speed ball milling (LSBM) and dual speed ball milling (DSBM) were adopted to grind Al powder. Average particle size of Al powder got reduced when the milling condition changed from LSBM to HSBM. Pallets were compacted at three different loads (520 MPa, 694 MPa and 867 MPa) followed by sintering at 530 ℃.
More